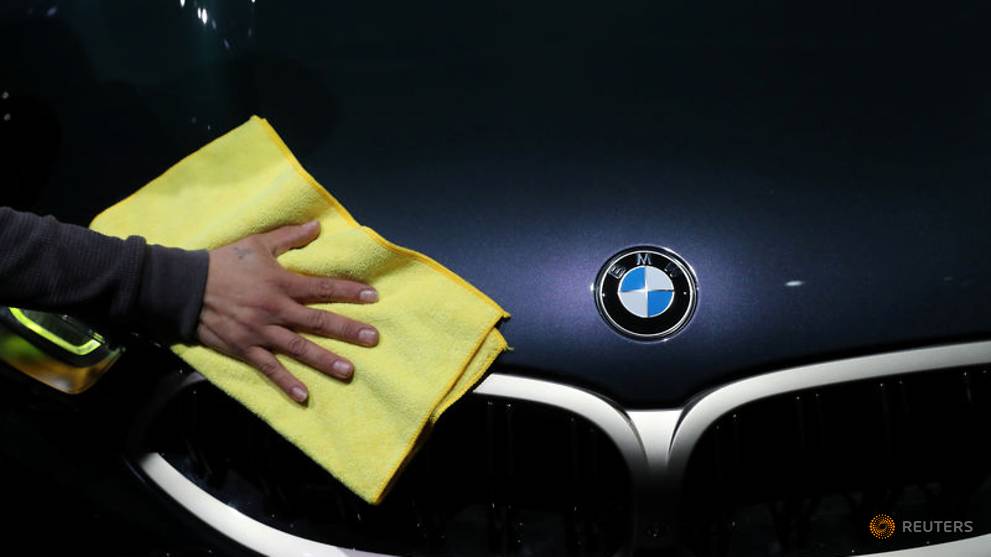
BMW Group announced today that it has secured its long-term lithium-ion battery cell needs for upcoming plug-in electric cars.
The German manufacturer selected two manufacturers, with whom BMW had already partnered:
- Chinese Contemporary Amperex Technology Co. Limited (CATL)
- South Korean Samsung SDI
In total, BMW ordered more than €10 Billion ($11 Billion) worth of cells by 2031.
In the case of CATL, BMW Group increases the previously announced (in mid-2018) order of €4 billion to €7.3 billion.
€4.5 billion will fall directly on BMW Group, while the remaining €2.8 billion will be used by the Chinese joint venture BMW Brilliance Automotive Ltd. (BBA) joint venture in Shenyang.
To fulfill the contract (2020-2031), CATL is building its first European manufacturing plant in Erfurt, Germany.
The original CATL order volume of four billion euros announced in mid-2018 will now be increased to 7.3 billion euros (contract duration from 2020 to 2031), with 4.5 billion euros for the BMW Group and 2.8 billion euros for the Chinese production site of the BMW Brilliance Automotive Ltd. (BBA) joint venture in Shenyang. The BMW Group is the first customer of the CATL battery cell plant currently under construction in Erfurt, Germany. “We strongly supported and played an active part in establishing CATL in Germany,” said Dr. Andreas Wendt, member of the Board of Management of BMW AG responsible for Purchasing and Supplier Network.
In the case of Samsung SDI (the main supplier for BMW so far), the supply contract was extended from 2021 to 2031. The deal is worth €2.9 billion.
“The BMW Group has also signed a long-term supply contract for its fifth-generation electric drive trains with its second battery cell supplier, Samsung SDI. The contract, with value of 2.9 billion euros, extends from 2021 to 2031. “In this way, we are securing our long-term battery cell needs. Every cell generation is awarded in global competition to the leading manufacturer from both a technology and a business perspective. This ensures we always have access to the best possible cell technology,” Wendt announced at a supplier event today in Seoul, South Korea.”
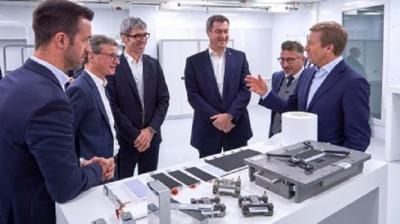
BMW intends to use CATL and Samsung SDI batteries in the upcoming fifth-generation electric drive trains, from 2021 on.
Additionally, BMW intends to directly source cobalt and lithium, which will then be made available for CATL and Samsung SDI.
“The BMW Group will source the cobalt needed as a key raw material for cell production directly from mines in Australia and Morocco and make it available to CATL and Samsung SDI. The same applies to lithium, which the BMW Group will also source directly from mines, including from Australia. This gives the company full transparency over where both raw materials come from. Compliance with environmental standards and respect for human rights have the highest priority. The BMW Group’s fifth-generation electric drive trains from 2021 on will also be produced entirely without using rare earths. “This means we will no longer be dependent on their availability,” explained Wendt.”
The battery cells from the supplier are used to assemble the modules and packs at several BMW plants:
- Dingolfing, Germany
- Spartanburg, USA
- Shenyang, China, at the BMW Brilliance Automotive Ltd. (BBA) plant
- Thailand, in partnership with the Dräxlmaier Group, one of its long-term automotive suppliers.
Together with the all-new R&D facility in Munich, and additional partnership deals with Northvolt and Umicore, BMW has in place a strong foundation for mass-electrification.
“The BMW Group possesses extensive in-house expertise throughout the entire value chain for battery cell technology. In-house battery production takes place at BMW Group Plants Dingolfing (Germany) and Spartanburg (USA), and at the BBA plant in Shenyang (China). The BMW Group has also localised battery production in Thailand and is working with the Dräxlmaier Group in this area.
On 14 November, the company opened its Battery Cell Competence Centre in Munich. The aim of the competence centre is to advance battery cell technology and introduce it into production processes. The company invested a total of 200 million euros in the location, which is set to create up to 200 jobs. The production of battery cell prototypes makes it possible to analyse and fully understand cell value creation processes. “Whether we then produce the cells ourselves at a later date, will largely depend on how the supplier market develops,” according to Wendt.
The BMW Group has formed a joint technology consortium with Swedish battery manufacturer Northvolt and Umicore, a Belgian developer of battery materials, for the purpose of developing the cell technology crucial to electromobility. The cooperation will focus on creating a complete, sustainable value chain for battery cells in Europe, extending from development and production all the way to recycling. Recycling of battery components plays a decisive role in closing the materials cycle as far as possible and maximising reuse of raw materials as demand for battery cells grows.”
The plan for 2023 is to offer 25 plug-in electric models, out of which more than half will be BEVs.
Courtesy: InsideEVs